ツーショット (デュアルショット、ダブルショット、マルチショット、オーバーモールディングとも呼ばれます) は、2 つの異なるプラスチック樹脂を 1 回の加工サイクルで一緒に成形するプラスチック成形プロセスです。
ツーショット射出成形アプリケーション
ツーショット射出成形は、特に大量生産シナリオにおいて、複雑、多色、複数材料のプラスチック製品にとって理想的なプラスチック成形プロセスです。当社の射出成形センターでは、自動車・家電分野の設計・製造を中心に、各種射出成形に対応しております。
消費財から自動車に至るまで、ツーショット成形部品はほぼすべての業界で使用されていますが、最も一般的に使用されるのは次のような用途です。
可動セグメントまたはコンポーネント
ソフトグリップを備えた硬質基板
振動または音響の減衰
表面の説明または識別
マルチカラーまたはマルチマテリアルのコンポーネント
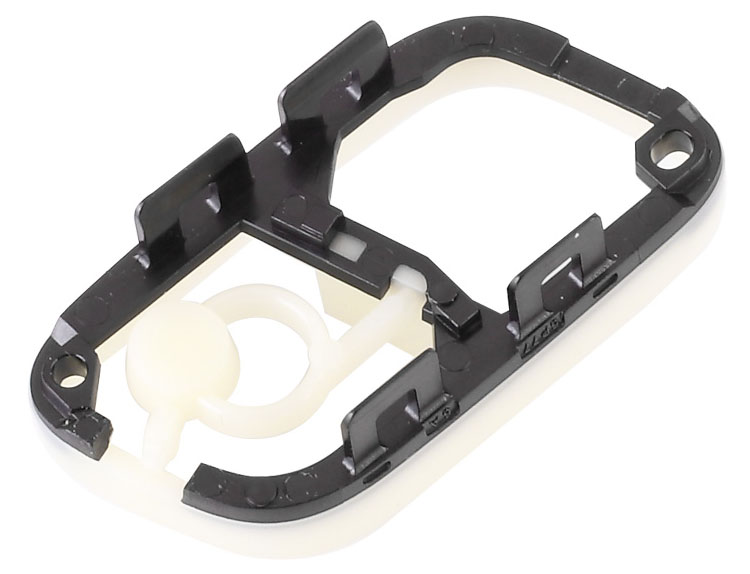
ツーショット成形のメリット
他のプラスチック成形方法と比較して、ツーショットは最終的には複数のコンポーネントからなるアセンブリを製造するためのよりコスト効率の高い方法です。その理由は次のとおりです。
部品の統合
ツーショット射出成形により、完成したアセンブリのコンポーネントの数が減り、追加の部品番号ごとに平均 40,000 ドルの開発、エンジニアリング、検証コストが削減されます。
効率の向上
ツーショット成形では、複数のコンポーネントを 1 つのツールで成形できるため、部品の実行に必要な労力が削減され、成形プロセス後にコンポーネントを溶接したり接合したりする必要がなくなります。
品質の向上
ツーショットは 1 つのツール内で実行されるため、他の成形プロセスよりも低い公差、高レベルの精度と再現性、およびスクラップ率の削減が可能になります。
複雑な成形品
ツーショット射出成形では、他の成形プロセスでは実現できない機能を実現するために、複数の材料を組み込んだ複雑な金型設計を作成できます。
ツーショット射出成形はコスト効率が高い
2 段階のプロセスでは、最初の金型を回転させて邪魔にならないようにし、2 番目の互換性のある熱可塑性プラスチックを 2 番目の金型に挿入できるように製品の周囲に 2 次金型を配置する 1 つのマシン サイクルのみが必要です。この技術では、個別のマシンサイクルではなく 1 つのサイクルのみを使用するため、生産実行にかかるコストが削減され、最終製品の製造に必要な従業員の数が減り、実行ごとにより多くのアイテムを納品できます。また、ラインでさらに組み立てる必要がなく、材料間の強力な結合が保証されます。
ツーショット注射サービスをお探しですか?
当社は過去 30 年をかけて、ツーショット射出成形の技術と科学を習得してきました。当社は、プロジェクトの構想から生産までを合理化するために必要な設計、エンジニアリング、社内ツールの機能を備えています。また、財務的に安定した企業として、当社はお客様の会社とツーショットのニーズの成長に合わせて生産能力を拡大し、事業を拡大する準備ができています。
ツーショット注射に関するよくある質問
ツーショット射出成形プロセスは 2 つのフェーズで構成されます。最初の段階は、従来のプラスチック射出成形技術と似ています。これには、最初のプラスチック樹脂のショットを金型に注入して、周囲に成形する他の材料の基板を作成することが含まれます。次に、基板を固化させて冷却した後、他の型チャンバーに移します。
基板の搬送方法が 2 ショット射出成形の速度に影響する可能性があることに注意することが重要です。手動による移送やロボットアームの使用は、回転面による移送よりも時間がかかることがよくあります。ただし、回転プレーンを使用するとコストが高くなり、大量生産の場合はより効率的になる可能性があります。
第 2 段階には、第 2 の材料の導入が含まれます。金型が開くと、基板を保持している金型の部分が 180 度回転して、射出成形ノズルと他の金型チャンバーに接触します。基板を所定の位置に配置したら、エンジニアは 2 番目のプラスチック樹脂を射出します。この樹脂は基材と分子結合を形成し、しっかりと保持します。2 番目の層も、最終コンポーネントを取り出す前に冷却されます。
金型の設計は、成形材料間の接着のしやすさに影響を与える場合があります。したがって、機械工やエンジニアは、接着を容易にし、欠陥を防ぐために、金型を正しく位置合わせする必要があります。
ツーショット射出成形により、ほとんどの熱可塑性プラスチック製品の品質がいくつかの方法で向上します。
見た目の美しさの向上:
アイテムは、さまざまな色のプラスチックやポリマーで作られていると、見た目も良くなり、消費者にとってより魅力的になります。複数の色や質感を使用すると、商品がより高価に見えます
人間工学の改善:
このプロセスではソフトタッチの表面を使用できるため、結果として得られるアイテムには人間工学に基づいて設計されたハンドルやその他のパーツを付けることができます。これは、工具、医療機器、その他の手持ちアイテムにとって特に重要です。
強化されたシール機能:
シリコーンプラスチックやその他のゴム状材料がガスケットや強力なシールを必要とするその他の部品に使用されている場合に、より優れたシールを実現します。
硬質ポリマーと軟質ポリマーの組み合わせ:
ハードポリマーとソフトポリマーの両方を組み合わせることができ、最小の製品であっても優れた快適性と実用性を実現します。
位置ずれの減少:
オーバーモールディングや従来のインサートプロセスと比較して、位置ずれの数を大幅に減らすことができます。
複雑な金型設計:
これにより、メーカーは、他のプロセスでは効果的に接着できない複数の材料を使用して、より複雑な金型設計を作成できるようになります。
非常に強い絆:
作成された結合は非常に強力であり、より耐久性があり、より信頼性が高く、より長寿命の製品が生まれます。
ツーショット技術の欠点は次のとおりです。
高い工具コスト
ツーショット射出成形には、綿密かつ慎重な設計、テスト、および金型ツールが必要です。初期設計とプロトタイピングは、CNC 加工または 3D プリントによって行うことができます。その後、金型ツールの開発が続き、目的の部品のレプリカの作成に役立ちます。最終生産が開始される前に、プロセスの効率性を確保するために、広範な機能テストと市場テストが行われます。したがって、この射出成形プロセスにかかる初期コストは通常高額になります。
小規模な生産では費用対効果が低い可能性があります
この技術に関連するツールは複雑です。また、次の生産を行う前に、以前の材料を機械から取り除く必要もあります。その結果、セットアップ時間が非常に長くなる可能性があります。したがって、小規模なランにツーショット技術を使用するとコストが高すぎる可能性があります。
部品設計の制限事項
ツーショットプロセスは、従来の射出成形ルールに従います。したがって、このプロセスでは依然としてアルミニウムまたはスチールの射出成形金型が使用されており、設計の繰り返しが非常に困難になっています。ツールキャビティのサイズを小さくすることは困難な場合があり、場合によっては製品のバッチ全体を廃棄することになります。その結果、コスト超過が発生する可能性があります。