Two-shot, also referred to as dual-shot, double-shot, multi-shot and overmolding, is a plastic molding process in which two different plastic resins are molded together in a single machining cycle.
Two-Shot Injection Molding Applications
Two-shot injection molding is the ideal plastic molding process for complex, multi-color, and multi-material plastic products, especially in high-volume production scenarios. Our injection molding center is able to offer various types of injection injection, but mainly specializing in the design and manufacturing for automotive and home appliance fields.
From consumer goods to automotive, two-shot molded components are used in nearly every industry, but are most commonly found in applications requiring the following:
Movable segments or components
Rigid substrates with soft grips
Vibration or acoustic dampening
Surface descriptions or identifications
Multi-color or multi-material components
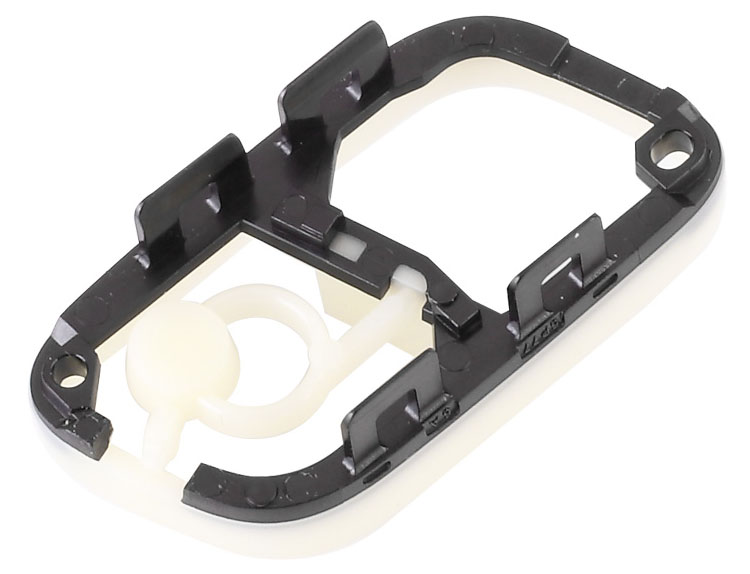
Benefits of Two-Shot Molding
Compared to other methods of plastic molding, two-shot is ultimately a more cost-efficient way of producing an assembly with multiple components. Here’s why:
Part Consolidation
Two-shot injection molding reduces the number of components in a finished assembly, eliminating an average of $40K in development, engineering, and validation costs associated with each additional part number.
Improved Efficiency
Two-shot molding allows multiple components to be molded with a single tool, reducing the amount of labor needed to run your parts and eliminating the need to weld or join components after the molding process.
Improved Quality
Two-shot is carried out within a single tool, allowing for lower tolerances than other molding processes, a high level of accuracy and repeat-ability, and reduced scrap rates.
Complex Moldings
Two-shot injection molding allows for the creation of complex mold designs that incorporate multiple materials for functionality that cannot be achieved through other molding processes.
Two-Shot Injection Molding Is Cost-Effective
The two-step process needs only one machine cycle, rotating the initial mold out of the way and putting the secondary mold around the product so that the second, compatible thermoplastic can be inserted into the second mold. Because the technique uses only one cycle instead of separate machine cycles, it costs less for any production run and requires fewer employees to make the finished product while delivering more items per run. It also ensures a strong bond between the materials without the need for further assembly down the line.
Are you looking for Two-Shot Injection services?
We’ve spent the past 30 years mastering the art and science of two-shot injection molding. We have the design, engineering, and in-house tooling capabilities you need to streamline your project from conception to production. And as a financially stable company, we’re prepared to expand capacity and scale operations as your company and your two-shot needs grow.
FAQ For Two-Shot Injection
The two-shot injection molding process consists of two phases. The first phase is similar to the conventional plastic injection molding technique. It involves injecting a shot of the first plastic resin into the mold to create the substrate for the other material (s) to be molded around. The substrate is then allowed to solidify and cool before transferring to the other mold chamber.
It is important to note that the method of transferring the substrate can affect the speed of 2-shot injection molding. Manual transfers or the use of robotic arms often take longer than transferring with a rotary plane. However, using rotary planes is more expensive and may be more efficient for high-volume productions.
The second phase involves the introduction of the second material. Once the mold opens, the part of the mold holding the substrate will rotate 180 degrees to meet the injection molding nozzle and the other mold chamber. With the substrate in place, the engineer injects the second plastic resin. This resin forms a molecular bond with the substrate to create a firm hold. The second layer is also allowed to cool before ejecting the final component.
Mold design may affect the ease of bonding between the molding materials. Therefore, machinists and engineers must ensure the correct alignment of molds to ensure easy adhesion and prevent defects.
Two-shot injection molding enhances the quality of most thermoplastic items in several ways:
Improved esthetics:
Items look better and are more appealing to the consumer when they are crafted of different colored plastics or polymers. The merchandise looks more expensive if it utilizes more than one color or texture
Improved ergonomics:
Because the process allows for the use of soft-touch surfaces, the resulting items can have ergonomically designed handles or other parts. This is particularly important for tools, medical devices, and other hand-held items.
Enhanced sealing capabilities:
It provides for a better seal when silicone plastics and other rubbery materials are used for gaskets and other parts that require a strong seal.
Combination of hard and soft polymers:
It lets you combine both hard and soft polymers for outstanding comfort and utility for even the smallest of products.
Reduced misalignments:
It can greatly reduce the number of misalignments when compared to over-molding or more traditional insert processes.
Complex mold designs:
It enables manufacturers to create more complex mold designs using multiple materials that can’t be effectively bonded using other processes.
Exceptionally strong bond:
The bond created is exceptionally strong, creating a product that is more durable, more reliable, and with longer life.
The following are the drawbacks of the two-shot technique:
High Tooling Costs
Two-shot injection molding involves in-depth and careful designing, testing, and mold tooling. Initial designing and prototyping may be done via CNC machining or 3D printing. Then the development of mold tooling follows, helping to create replicas of the intended part. Extensive functional and market testing is done to ensure the efficiency of the process before final production begins. Therefore, the initial costs involved in this injection molding process are usually high.
May Not Be Cost-Effective for Small Production Runs
The tooling involved in this technique is complex. There is also a need to remove previous materials from the machine before the next production run. As a result, setup time may be quite long. Therefore, using the two-shot technique for small runs may be too expensive.
Part Design Restrictions
The two-shot process follows the traditional injection molding rules. Therefore, aluminum or steel injection molds are still used in this process, making design iterations quite difficult. Reducing tool cavity size may be difficult and sometimes result in scrapping the entire batch of product. As a result, you may be incurring cost overruns.