The physical vapor deposition (PVD) process is a group of thin film processes in which a material is converted into its vapor phase in a vacuum chamber and condensed onto a substrate surface as a weak layer. PVD can be used to apply a wide variety of coating materials such as metals, alloys, ceramics, and other inorganic compounds. Possible substrates include metals, glass, and plastics. PVD process represents a versatile coating technology, applicable to an almost unlimited combination of coating substances and substrate materials.
PVD classification
It is broadly grouped into three categories:
Vacuum evaporation
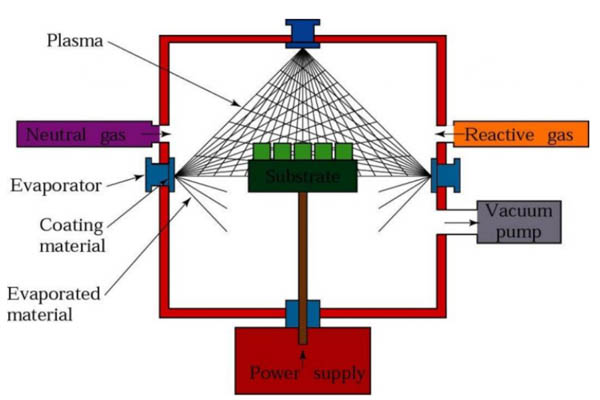
Vacuum evaporation process
Sputtering
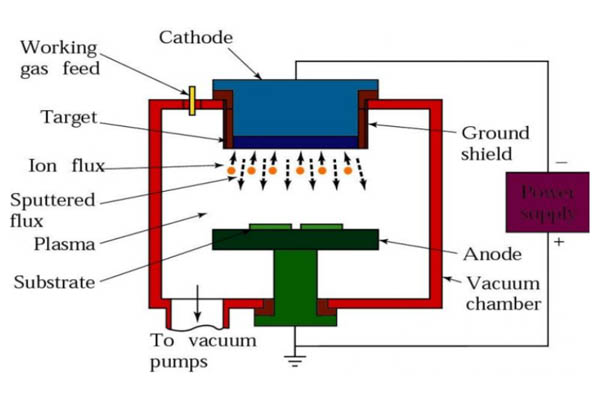
Sputtering process
Ion plating
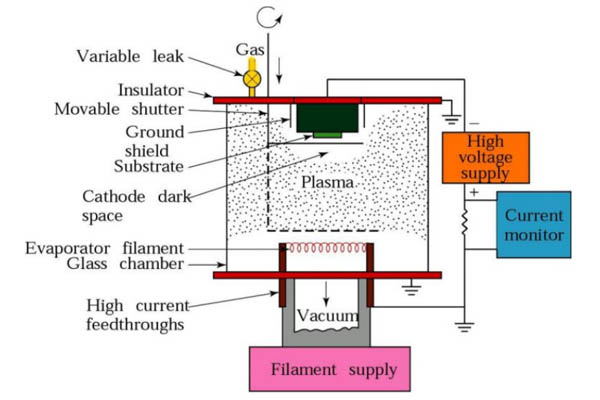
Ion plating process
Below table 1 presents a summary of these processes.
S.no |
PVD process |
Features and Comparisons |
Coating materials |
1 |
Vacuum evaporation |
Equipment is relatively low-cost and simple; deposition of compounds is difficult; coating adhesion not as good as other PVD processes. | Ag, Al, Au, Cr, Cu, Mo, W |
2 |
Sputtering |
Better throwing power and coating adhesion than vacuum evaporation can coat compounds, slower deposition rates, and more difficult process control than vacuum evaporation. | Al2O3, Au, Cr, Mo, SiO2, Si3N4, TiC, TiN |
3 |
Ion plating |
Best coverage and coating adhesion of PVD processes, most complex process control, higher deposition rates than sputtering. | Ag, Au, Cr, Mo, Si3N4, TiC, TiN |
In summary, all physical vapor deposition processes consist of the following steps:
1. Synthesis of the coating vapor,
2. Vapor transport to the substrate, and
3. Condensation of gases onto the substrate surface.
These steps are carried out inside a vacuum chamber, so evacuation of the chamber must precede the actual PVD process.
Application of PVD
1.Applications include thin decorative coatings on plastic and metal parts such as trophies, toys, pens, and pencils, watch cases, and interior trim in automobiles.
2.The coatings are thin films of aluminum (around 150nm) coated with clear lacquer to give a high gloss silver or chrome appearance.
3.Another use of PVD is to apply anti-reflection coatings of magnesium fluoride (MgF2) onto optical lenses.
4.PVD is applied in the fabrication of electronic devices, principally for depositing metal to form electrical connections in integrated circuits.
5.Finally, PVD is widely used to coat titanium nitride (TiN) onto cutting tools and plastic injection molds for wear resistance.
Pros
1. PVD coatings are sometimes harder and more corrosion-resistant than coatings applied by electroplating processes. Most coatings have high temperature and good impact strength, excellent abrasion resistance, and are so durable that protective topcoats are rarely necessary.
2. Ability to utilize virtually any type of inorganic and some organic coating materials on an equally diverse group of substrates and surfaces using a wide variety of finishes.
3. More environmentally friendly than traditional coating processes such as electroplating and painting.
4. More than one technique can be used to deposit a given film.
Cons
1. Specific technologies can impose constraints; for example, the line-of-sight transfer is typical of most PVD coating techniques, however, some methods allow full coverage of complex geometries.
2. Some PVD technologies run at high temperatures and vacuums, requiring special attention from operators.
3. A cooling water system is often required to dissipate large heat loads.
If you’d like to understand more PVD knowledge, please feel free to contact us at any moment.
About CheeYuen
Established in Hong Kong in 1969, CheeYuen is a solution provider for plastic part manufacturing and surface treatment. Equipped with advanced machines and production lines (1 tooling and injection molding center, 2 electroplating lines, 2 painting lines, 2 PVD line and others) and led by a committed team of experts and technicians, CheeYuen Surface Treatment provides a turnkey solution for chromed, painting & PVD parts, from tool design for manufacturing (DFM) to PPAP and eventually to finished part delivery across the globe.
Certified by IATF16949, ISO9001 and ISO14001 and audited with VDA 6.3 and CSR, CheeYuen Surface Treatment has become a widely-acclaimed supplier and strategic partner of a great number of well-known brands and manufacturers in automotive, appliance, and bath product industries, including Continental, ALPS, ITW, Whirlpool, De’Longhi and Grohe, etc.
Have comments regarding this post or topics that you would like to see us cover in the future?
Send us an email at :peterliu@cheeyuenst.com
Post time: Oct-07-2023