Injection Molding Capabilitie
Our injecttion molding center has 38 sets of one-shot, two-shot, and three-shot Sumitono,Demag and HaiTian electric injection machines of 50T to 750T, each one equipped with a Japanese Yunshin robot arm and Kawata mold temperature controllers, independently monitoring each core and cavity mold to ensure part precision and production stability. The molding shop also features separate molding and labor areas with a centralized resin feeding system, which not only provides a pleasat working environment,but also guarantees work efficiency and production quality.
Beyond this, CheeYuen Plastic Parts(Huizhou)Co., Ltd, affiliated with CheeYuen Industrial, possesses another 300 injection molding machines of 30T to 1600T. These brands include DEMAG, FANUC, MITSUBISHI and HAITIAN, all ready to meet different customers's demands.We use many kinds of plastic such as PP, PE, ABS, PC-ABS, PA, PPS, POM, PMMA, etc.
CheeYuen is a global leader in plastic injection molding services, and we provide a complete manufacturing solution, starting from raw material verification, tool making, component fabrication, finishing, and assessment. We always do our best to meet our customer requirement and customer satisfaction.
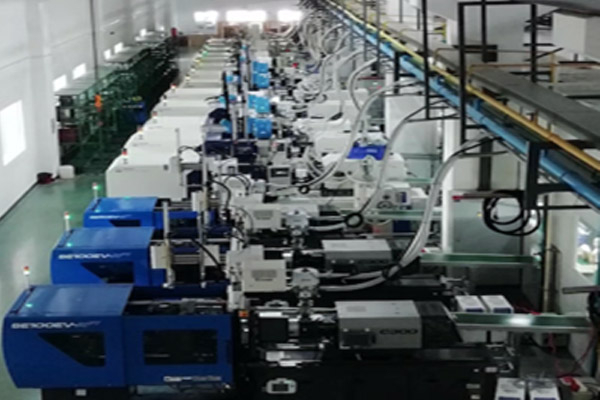
Injection Moulding’s Machine Fleet
The injection mold center owns more than 300 sets of one-shot and two-shot injection molding machines from 30T to 1600T, including brands like DEMAG, FANUC, TOSHIBA, and MITSUBISHI. Each molding machine is equipped with auxiliary molding devices.
The tooling center, equipped with Moldflow analysis and Mold Management System (MMS) software, one Japanese Makino machining center, one Swiss Charmilles EDM, one slow wire machine, and other manufacturing machines, some of whose machining accuracy up to 0.01mm, has become a professional precision mold manufacturing center with CAE/CAD/CAM integration.
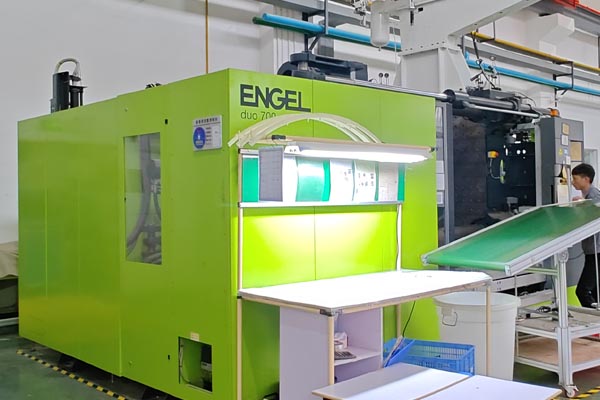
750t Injection Machine
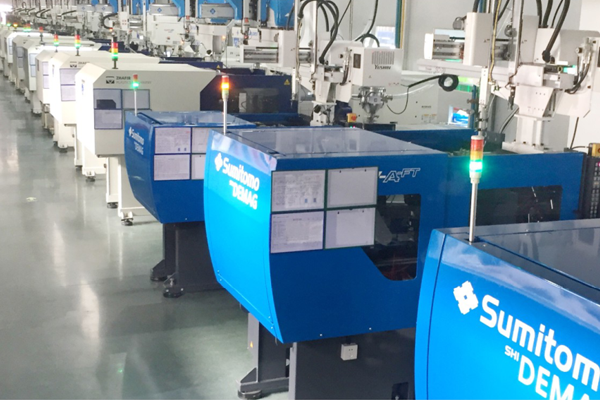
Injection Workshop
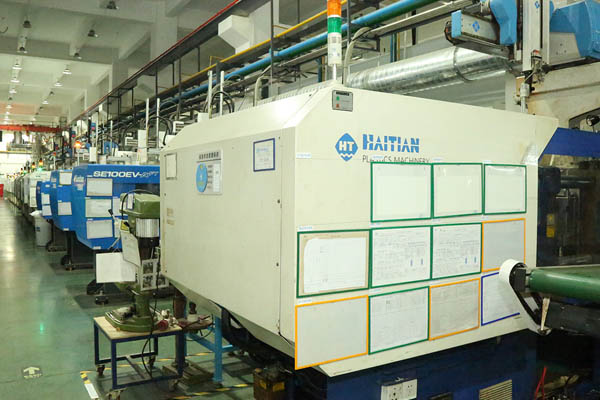
Molding Injection Machines
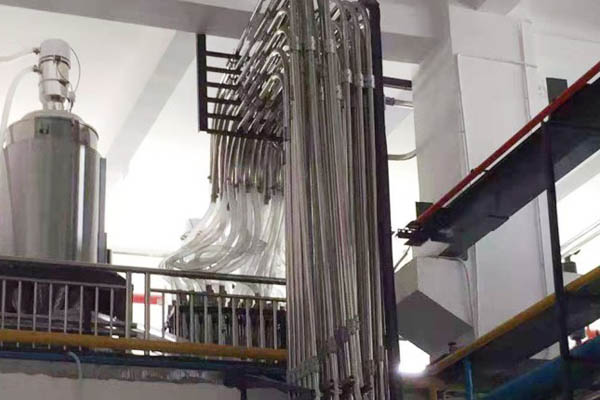
Centralized Feeding System
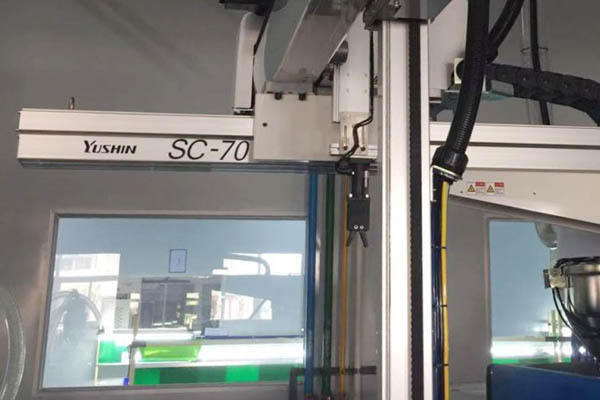
Japanese Yushin Robot Arm
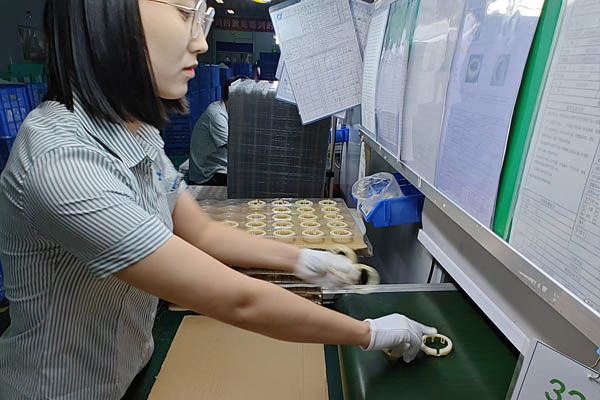
Molded Bezel De-Gating
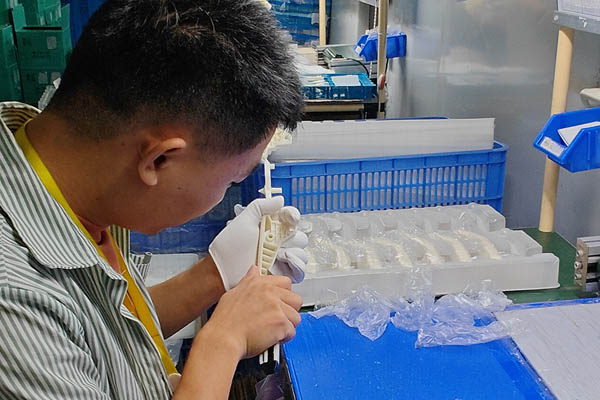
Auto Door Handle De-Gating
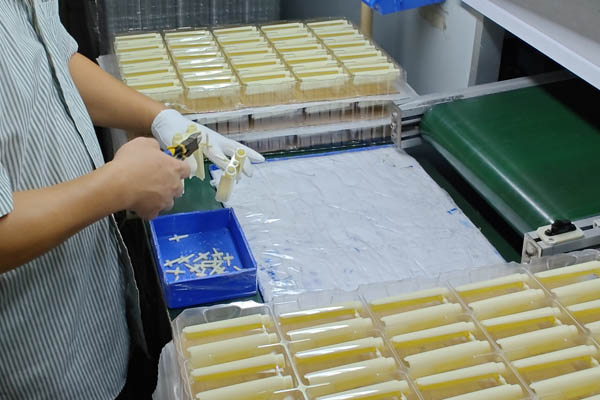
Coffee Machine Cover De-Gating
Injection moulding 30–1600 tonnes
Injection compression moulding
Compression moulding
Back injection moulding on textiles
2K injection moulding 100–1000 tonnes
Clean-room injection
Clean-room assembly
MACHINE (TONS) | MODEL | QTY (SETS) | MANUFACTURER | |
1 | 1600 | 1600MM3W340* | 1 | MITSUBISHI |
2 | 1200 | HTL1200 | 7 | HAITAI |
3 | 1000 | HTL1000 | 9 | HAITAI |
4 | 730 | HTL730 | 8 |
HAITAI |
5 | 650 | 650MGIII | 5 | MITSUBISHI |
6 | 550 | JSW-N550BII | 9 | JSW |
7 | 450 | 450MSIII | 9 | MITSUBISHI |
8 | 400 | JSW-N400BII | 7 | JSW |
9 | 350 | 350MSIII | 6 | MITSUBISHI |
10 | 300 | JSW-N300BII | 11 | JSW |
11 | 280 | IS280 | 5 | TOSHIBA |
12 | 240 | 240MSIII | 2 | MITSUBISHI |
13 | 200 | IS-200B | 9 | TOSHIBA |
14 | 180 | JEKS-180 | 2 | JSW |
15 | 175 | KS-175B | 2 | KAWAGUCHI |
16 | 160 | 160MSIII | 5 | MITSUBISHI |
17 | 150 | JSW-J150S | 3 | JSW |
18 | 140 | JSW-N140BII | 3 | JSW |
19 | 110 | KS-110B | 4 | KAWAGUCHI |
20 | 100 | S2000i 100A | 5 | FANUC |
21 | 80 | KM80 | 1 | KAWAGUCHI |
22 | 50 | KS-70 | 4 | KAWAGUCHI |
23 | 30 | S2000i 50A | 5 | FANUC |
Injection moulding
Well-established standard procedure for manufacturing of plastic parts.
The CheeYuen has injection moulding machines with clamping forces of 30-1600 tonnes.
Injection Compression Moulding
The philosophy of injection-compression mouldings – the injection of thermoplastic polymer melts into a slightly opened mould with simultaneous or subsequent compression by an additional clamping stroke.
We use a technology in which the additional stroke is accomplished via an integrated hydraulic booster inside the mould.
Compression moulding using ICM
Here, we use the injection moulding machine to create the compression.
First, the material is injected when the tool is open. When 80% of the tool is filled, the tool is closed and the final step is compression.
This method is commonly used for thin wall thicknesses and long flow paths.
(Creates less internal stress and reduced warpage.)
Back injection moulding on textiles
Multilayer polyester fabric inserted in tool.
Back injection with PC/ABS.
2K injection moulding
There are different methods for injecting two chemically compatible materials.
Rotating tool (genuine 2K solution optimum condition).
Rotating with index plate (genuine 2K solution optimum condition).
Move with robot into second insert (semi-genuine 2K solution).
Pre-produced part components put into 2nd mould and over-injected by second material (false 2K).
Inserts
Commonly used when high torque is required on threads/screw.
The inserts may be over-moulded or mounted after injection.
Why Choose Us?
A Global Leader in Plastic Chrome Plating Companies

With over 33 years of experience in the plastic chrome plating industry

We have a complete production process

We produce and provide OEM and REM customers

Product quality complies with international standards
Injection on Plastic Components
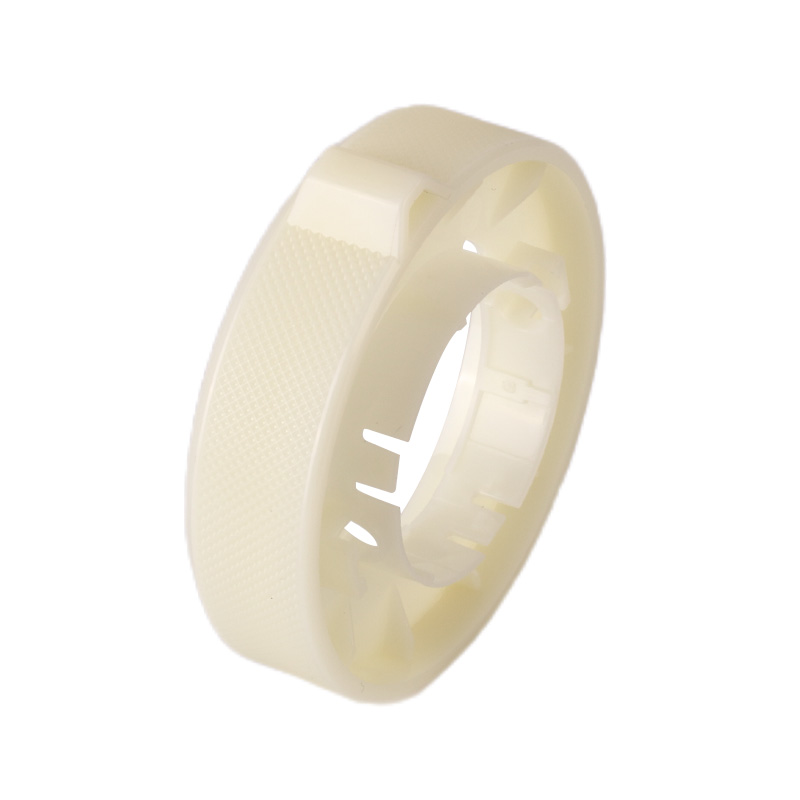
Abs Molded Kurled Ring
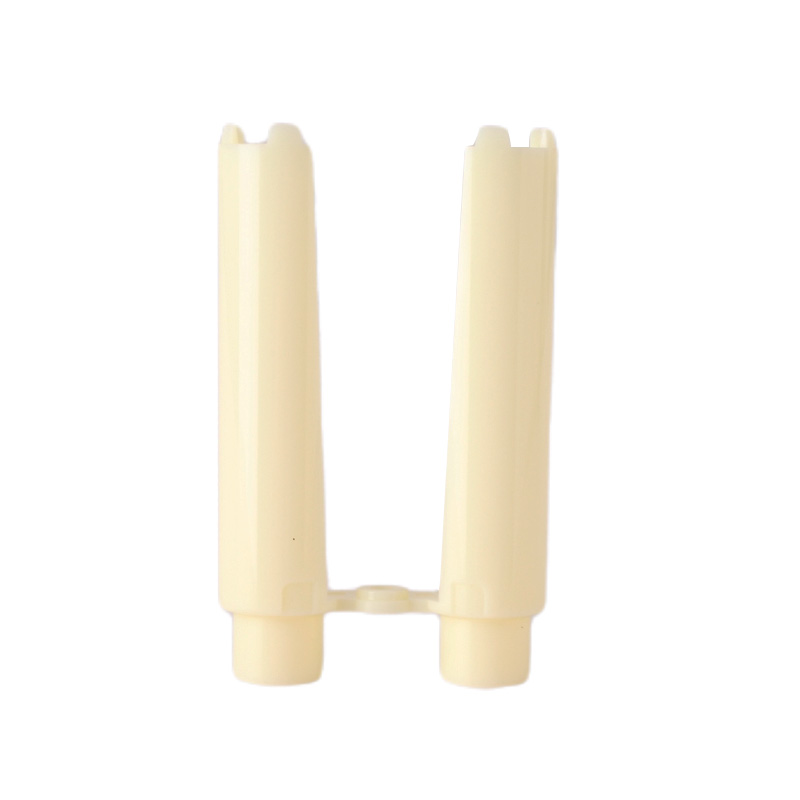
Molded Coffee Machine Cover
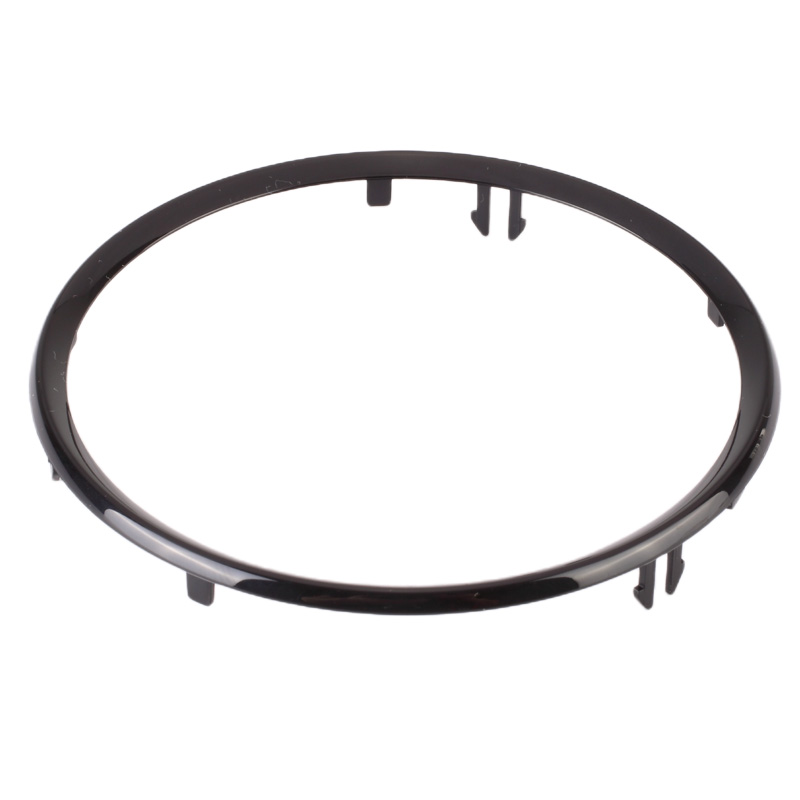
Grey Molded Dashboard Ring
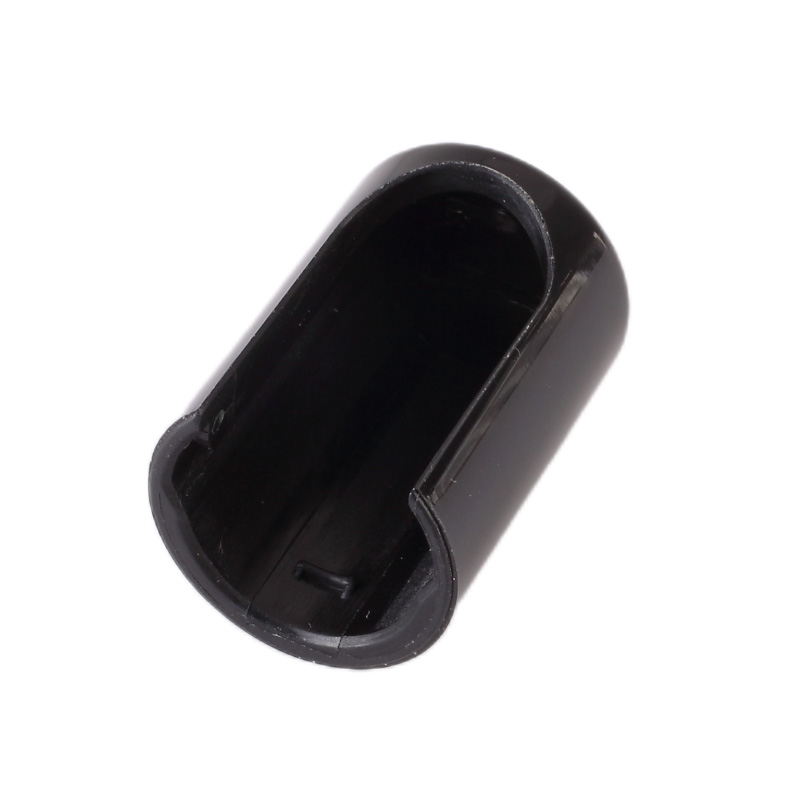
Coffee Machine Cap
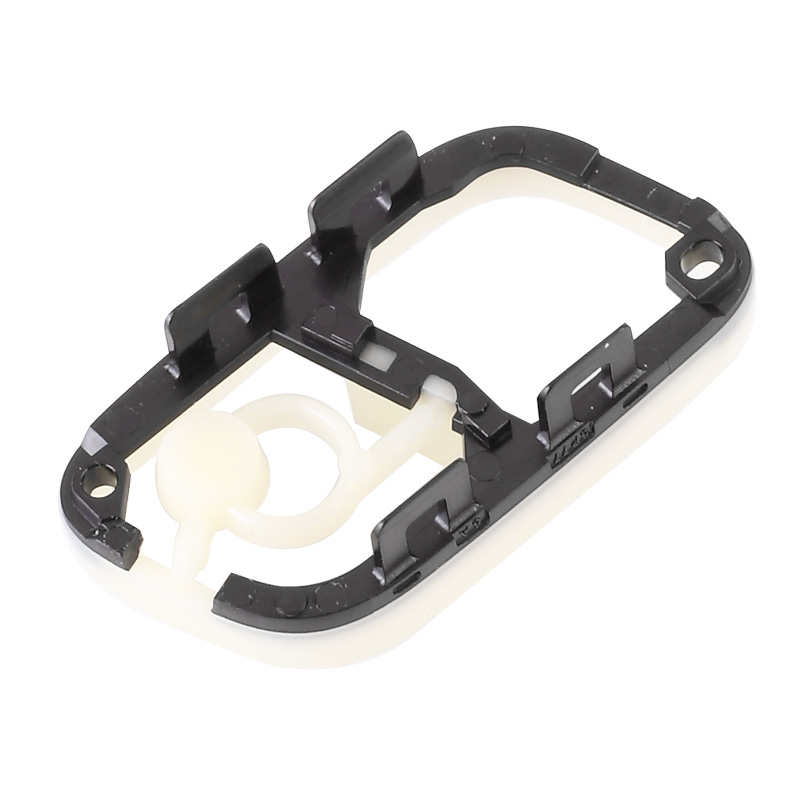
Key Fob Molded
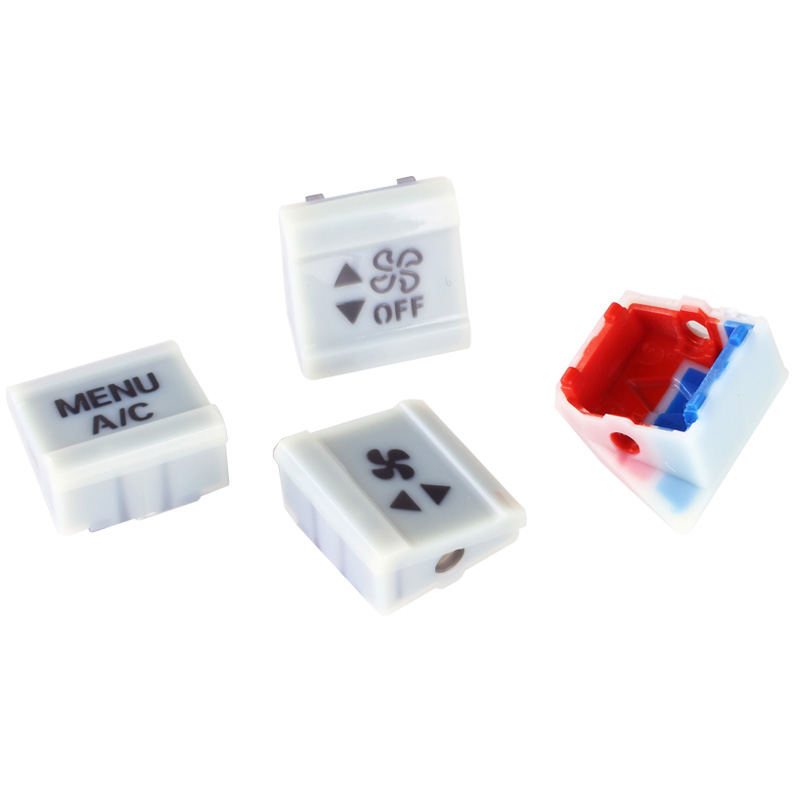
Molded Buttons with Tricolor
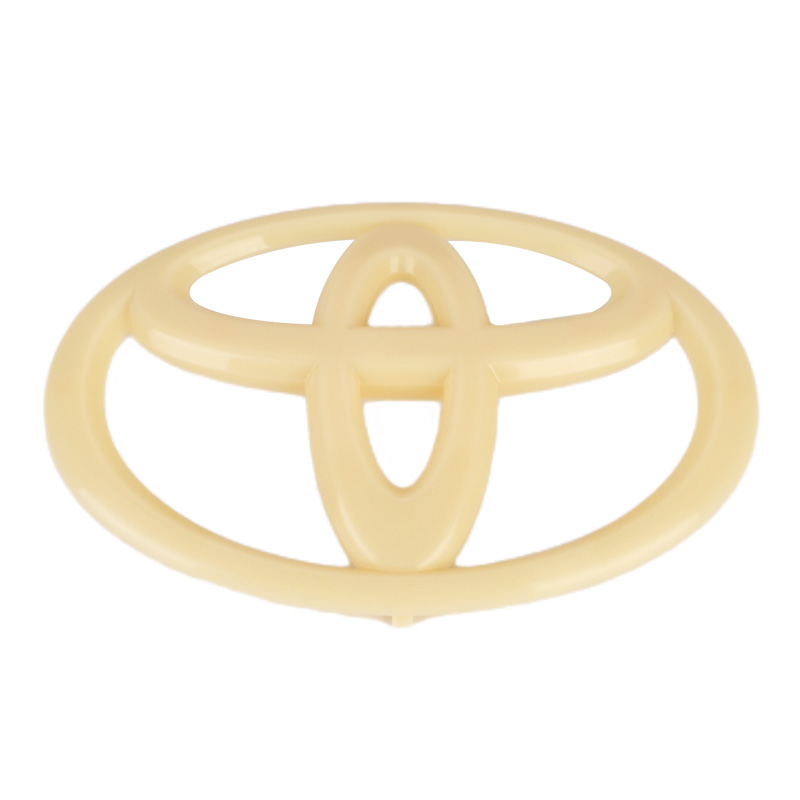
Molded Knurled Ring
People Also Asked:
Injection molding is a complex manufacturing process. Using a specialized hydraulic or electric machine, the process melts, injects and sets plastic into the shape of a metal mold that’s fitted into the machine.
Plastic injection molding is the most widely used components manufacturing process for a variety of reasons, including:
Flexibility: manufacturers can choose the mold design and type of thermoplastic that’s used for each component. This means the injection molding process can produce a variety of components, including parts that are complex and highly detailed.
Efficiency: once the process has been set up and tested, injection molding machines can produce thousands of items per hour.
Consistency: if the process parameters are tightly controlled, the injection molding process can produce thousands of components quickly at a consistent quality.
Cost-effectiveness: once the mold (which is the most expensive element) has been built, the cost of production per component is relatively low, particularly if created in high numbers.
Quality: whether manufacturers are looking for strong, tensile or highly detailed components, the injection molding process is able to produce them at a high quality repeatedly.
This cost-effectiveness, efficiency and component quality are just some of the reasons why many industries choose to use injection molded parts for their products.
Cost-effective way to create large numbers of parts
Injection molding is a cost-effective way to produce many parts, which makes it ideal for industries that need to make many items in a short amount of time.
Very precise
Injection molds are made with very tight tolerances and can produce parts with very little variation between them. This means that you can be sure that every part will be exactly the same as the next one, which is important if you’re looking for consistency in your products or if you need your product to fit together perfectly with another piece from another manufacturer’s line
The first stage of injection moulding is to create the mould itself. Most moulds are made from metal, usually aluminium or steel, and precision machined to match the features of the product they are to produce.
Once the mould has been created by the mould-maker, the material for the part is fed into a heated barrel and mixed using a helical shaped screw. Heating bands melt the material in the barrel and the molten metal or molten plastic material is then fed into the mould cavity where it cools and hardens, matching the shape of the mould. The cooling time can be reduced through the use of cooling lines that circulate water or oil from an external temperature controller. Mould tools are mounted on plate moulds (or ‘platens’), which open once the material has solidified so that ejector pins can eject the part from the mould.
Separate materials can be combined in one part in a type of injection moulding called a two-shot mould. This technique can be used to add a soft touch to plastic products, add colours to a part or produce items with different performance characteristics.
Moulds can be made of single or multiple cavities. Multiple cavity moulds can have identical parts in each cavity or can be unique to create parts of different geometries. Aluminium moulds are not best suited to high volume production or parts with narrow dimensional tolerances since they have inferior mechanical properties and can be prone to wear, deformation and damage due to the injection and clamping forces. While steel moulds are more durable they are also more expensive than aluminium moulds.
The injection moulding process requires careful design, including the shape and features of the part, the materials for the part and the mould and the properties of the moulding machine. As a result, there are various considerations that need to be taken into account when injection moulding.
There are a number of considerations to bear in mind before undertaking injection moulding:
1. Financial
The entry cost for injection moulding manufacture can be high – given the cost of the machinery and the moulds themselves.
2. Production Quantity
It is important to determine how many parts you wish to manufacture so as to decide whether injection moulding is the most cost-effective production method.
3. Design Factors
Minimising the number of parts and simplifying the geometry of your items will make injection moulding easier. In addition, the design of the mould tool is important to prevent defects during production.
4. Production Considerations
Minimising the cycle time will aid production as will using machines with hot runner moulds and well thought-out tooling. Such small changes and use of hot runner systems can equal production savings for your parts. There will also be cost savings from minimising assembly requirements, especially if you are producing many thousands of even millions of parts.
Injection moulding can be an expensive process, but there are several ways in which you can reduce mould costs, including:
Eliminate undercuts
Remove unnecessary features
Use a core cavity approach
Reduce cosmetic finishes
Design parts that self-mate
Modify and re-use existing moulds
Monitor DFM analysis
Use a multi cavity or family type of mould
Consider your part sizes
With over 85,000 commercial plastic material option available and 45 polymer families, there is a wealth of different plastics that can be used for injection moulding. Of these, the polymers can be broadly placed into two groups; thermosets and thermoplastics.
The most common types of plastic used are high-density polyethylene (HDPE) and low-density polyethylene (LDPE). Polyethylene offers a number of advantages including high ductility levels, good tensile strength, strong impact resistance, resistance to moisture absorption, and recyclability.
Other commonly used injection moulded plastics include:
1. Acrylonitrile Butadiene Styrene (ABS)
This tough, impact-resistant plastic is widely used across industry. With good resistance to acids and bases, ABS also offers low shrinkage rates and high dimensional stability.
2. Polycarbonate (PC)
This strong, impact resistant plastic has low shrinkage and good dimensional stability. A transparent plastic that is available in different optically clear grades, PC can provide a high cosmetic finish and good heat resistance.
3. Aliphatic Polyamides (PPA)
There are many different types of PPA (or nylons), each of which has its own advantages. Generally-speaking, nylons offer high strength and temperature resistance as well as being chemically resistant, apart from against strong acids and bases. Some nylons are abrasion resistant and offer good hardness and stiffness with good impact strength.
4. Polyoxymethylene (POM)
Commonly known as acetal, this plastic has high hardness, stiffness, strength and toughness. It also has good lubricity and is resistant to hydrocarbons and organic solvents. Good elasticity and slipperiness also provide advantages for some applications.
5. Polymethyl Methacrylate (PMMA)
PMMA, also known as acrylic, provides good optical properties, high gloss and scratch resistance. It also offers low shrinkage and less sink for geometries with thin and think sections.
6. Polypropylene (PP)
This inexpensive resin material delivers high impact resistance in certain grades but can be brittle in cold temperatures (in the case of propylene homopolymer). Copolymers offer greater resistance to impact while PP is also wear-resistant, flexible and can provide very high elongation, as well as being resistant to acids and bases.
7. Polybutylene Terephthalate (PBT)
Good electrical properties makes PBT ideal for power components as well as automotive applications. The strength ranges from moderate to high depending on glass fill, with unfilled grades being tough and flexible. PBT also shows fuels, oils, fats and many solvents, and it also doesn’t absorb flavours.
8. Polyphenylsulfone (PPSU)
A dimensionally stable material with high toughness, temperature and heat resistance, PPSU is also resistant to radiation sterilisation, alkalis and weak acids.
9. Polyether Ether Ketone (PEEK)
This high temperature, high-performance resin provides heat resistance and flame retardancy, excellent strength and dimensional stability, as well as good chemical resistance.
10. Polyetherimide (PEI)
PEI (or Ultem) offers high temperature resistance and flame retardancy, along with excellent strength, dimensional stability and chemical resistance.
Injection molding produces low scrap rates relative to traditional manufacturing processes like CNC machining which cut away substantial percentages of an original plastic block or sheet. This however can be a negative relative to additive manufacturing processes like 3D printing that have even lower scrap rates.
Waste plastic from injection molding manufacturing typically comes consistently from four areas:
The sprue
The runners
The gate locations
Any overflow material that leaks out of the part cavity itself (a condition called “flash”)
Thermoset material, such as an epoxy resin that cures once exposed to air, is a material that cures and would burn after curing if one attempt is made to melt it. Thermoplastic material, by contrast, is a plastic material that can be melted, cool and solidify, and then be melted again without burning.
With thermoplastic materials, they can be recycled and are used again. Sometimes this happens right on the factory floor. They grind up the sprues/runners and any reject parts. Then they add that material back into the raw material that goes into the injection molding press. This material is referred to as "re-grind".
Typically, quality control departments will limit the amount of regrind that is allowed to be placed back into the press. (Some performance properties of the plastic can degrade as it is molded over and over).
Or, if they have a lot of it, a factory can sell this re-grind to some other factory who can use it. Typically regrind material is used for low-quality parts that don't need high performance properties.